Projects
Caltech Aerospace Robotics & Controls Lab summer research Image Generation
As the Aerospace Corporation SURF Fellow at Caltech's Aerospace Robotics & Controls Lab under Professor Soon-Jo Chung, I engineered a deep Convolutional Neural Network driven, computer-vision-based pipeline which would implement an Extended Kalman Filter to execute space borne Angles-Only Navigation. To accomplish this, custom training was necessary to optimize the deep CNN for the task of spacecraft detection in close-proximity operations, and thus, generating realistic images of close-proximity spacecraft in orbit was necessary. To do this, I utilized Blender software to synthetically generate images of Earth as it would appear in orbit in random positions, at random times of day, with random weather conditions, etc. Using spacecraft models and Blender scripts, I then generated images of spacecraft in random poses and lighting conditions with transparent backgrounds. Then, I scraped the internet for images of spacecraft I did not have models for with transparent backgrounds. I wrote a script to re-size the scraped images and apply data augmentation techniques to them, artificially increasing the size of my dataset. Finally, I wrote a script to create the labeled dataset. The script created the labeled dataset by first extracting the rectangular bounding box coordinates from both the synthetic and scraped spacecraft images. Then, the script randomly combined the spacecraft images with the synthetically generated Earth background images. Finally, the script created a .txt file for each randomly generated spacecraft-Earth scene with the values necessary for training.


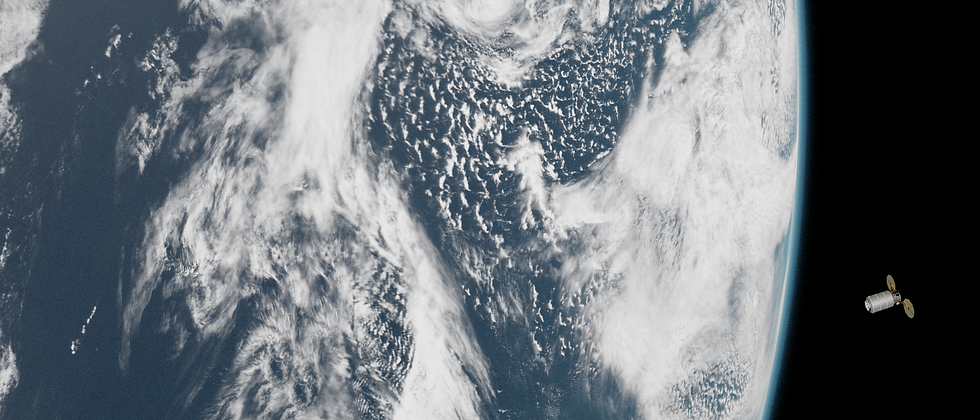

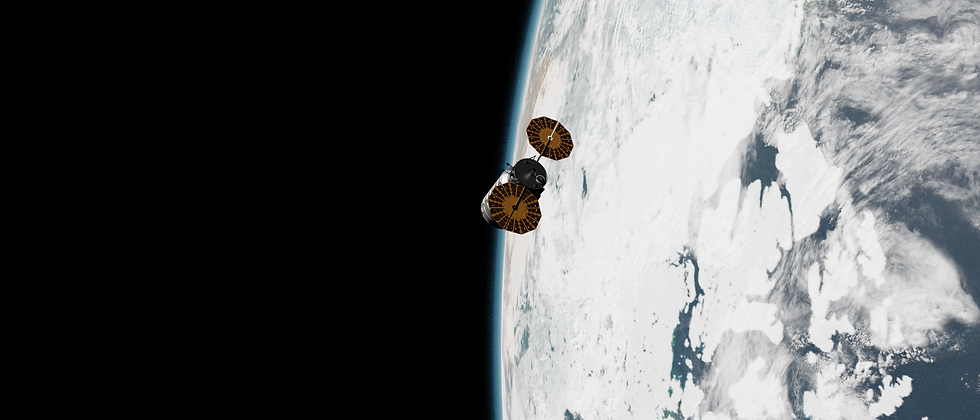

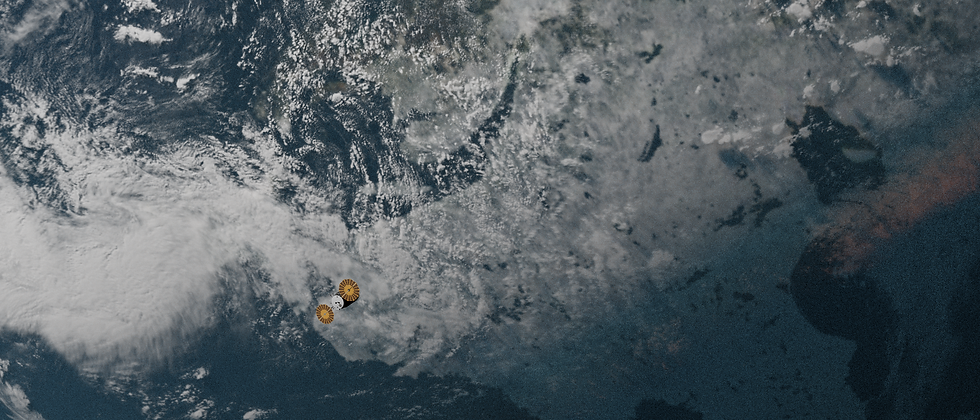


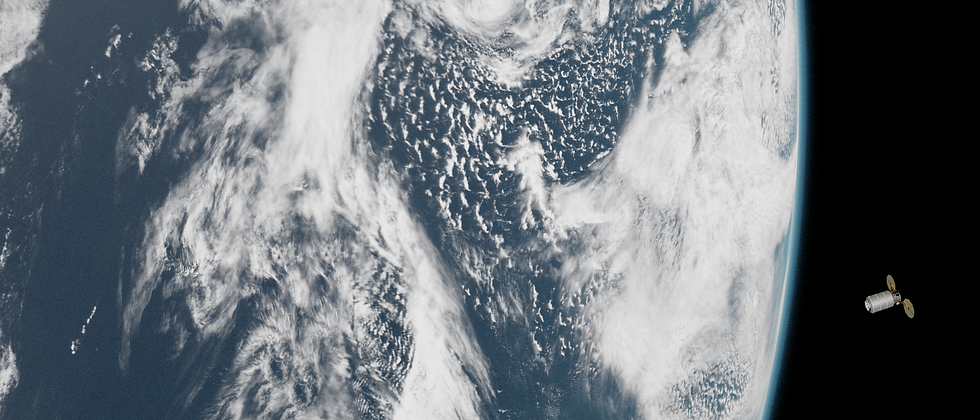

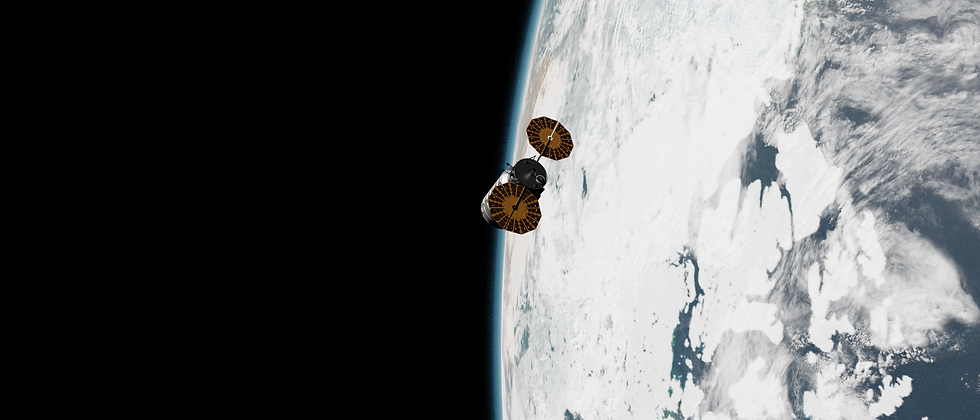

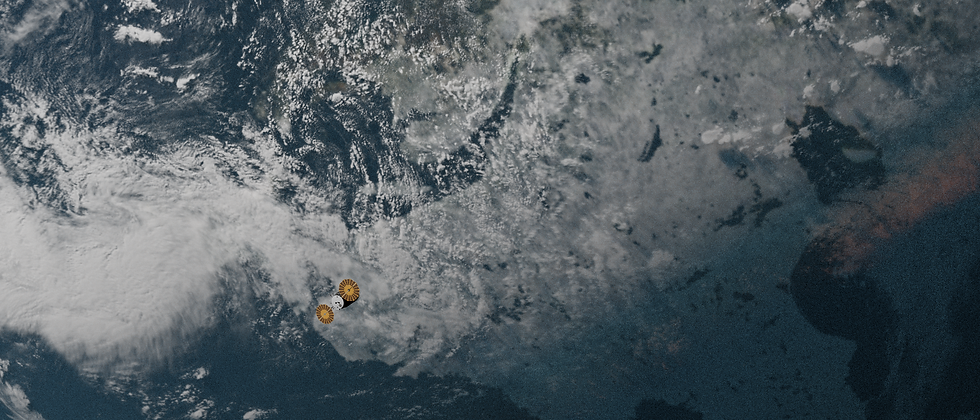
Caltech Aerospace Robotics & Controls Lab summer research Pipeline engineering
As the Aerospace Corporation SURF Fellow at Caltech's Aerospace Robotics & Controls Lab under Professor Soon-Jo Chung, I engineered a deep Convolutional Neural Network driven, computer-vision-based pipeline which would implement an Extended Kalman Filter to execute space borne Angles-Only Navigation. Once our deep CNN model had been trained and its performance validated, our pipeline had to be engineered. Since we were interested in the application of our angles-only navigation technique to real-life close-proximity operations, it was vital that I made our pipeline capable of interfacing with hardware while continuing to run in real-time. This necessity meant that the pipeline would utilize the Robotics Operating System 2 (ROS2). After implementing a ROS2 wrapper, translating detected bounding boxes into ROS2 messages and publishing to a ROS topic, I wrote custom ROS nodes to execute angles-only navigation. The first ROS node published the ground truth orientation of the chaser spacecraft as a Quaternion to a ROS topic. The second ROS node published the ground truth GPS location of the chaser spacecraft to another ROS topic. The third ROS node subscribed to both ROS topics and the ROS2-YOLOv5 wrapper’s ROS topic. This subscriber node implemented a time synchronizer object to filter messages by their timestamps, using the ground truth orientation and gps location of the chaser spacecraft along with the target spacecraft’s detected bounding box coordinates as the inputs to an EKF. The EKF then used this information to estimate the target spacecraft’s position and velocity.




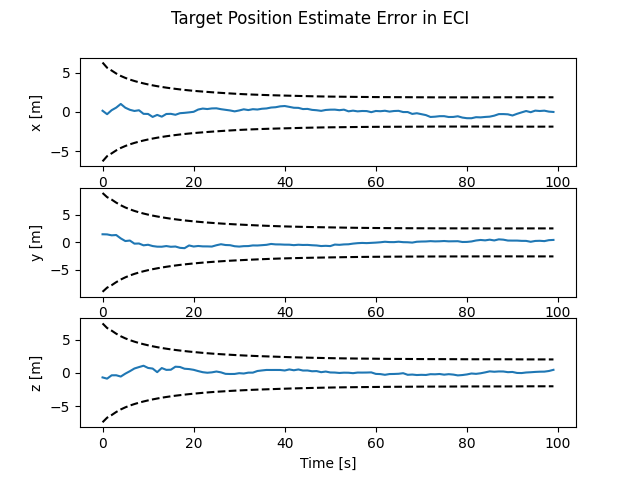




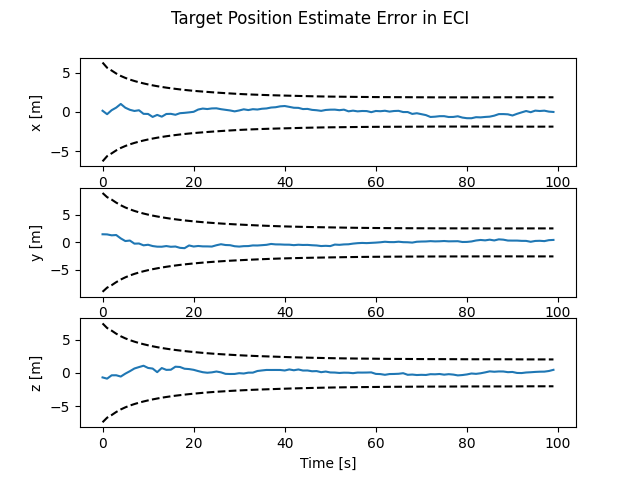
syntheon llc worst case scenario analysis & solidworks modeling
As a Mechanical Engineering Intern at Syntheon LLC I lead the LAA Exclusion System worst case scenario analysis and modeling. During this project I analyzed the LAA Exclusion System's SOLIDWORKS third angle projection drawings & identified which end of the specs would be the mechanically worst case scenario on the delivery system. After my analysis was confirmed I altered the delivery system’s SOLIDWORKS third angle projection drawings & CAD model to display the worst case scenario. These altered models were then sent to Design Automation Associates (DAA) for finite element analysis to determine the factor of safety in the worst case scenario.
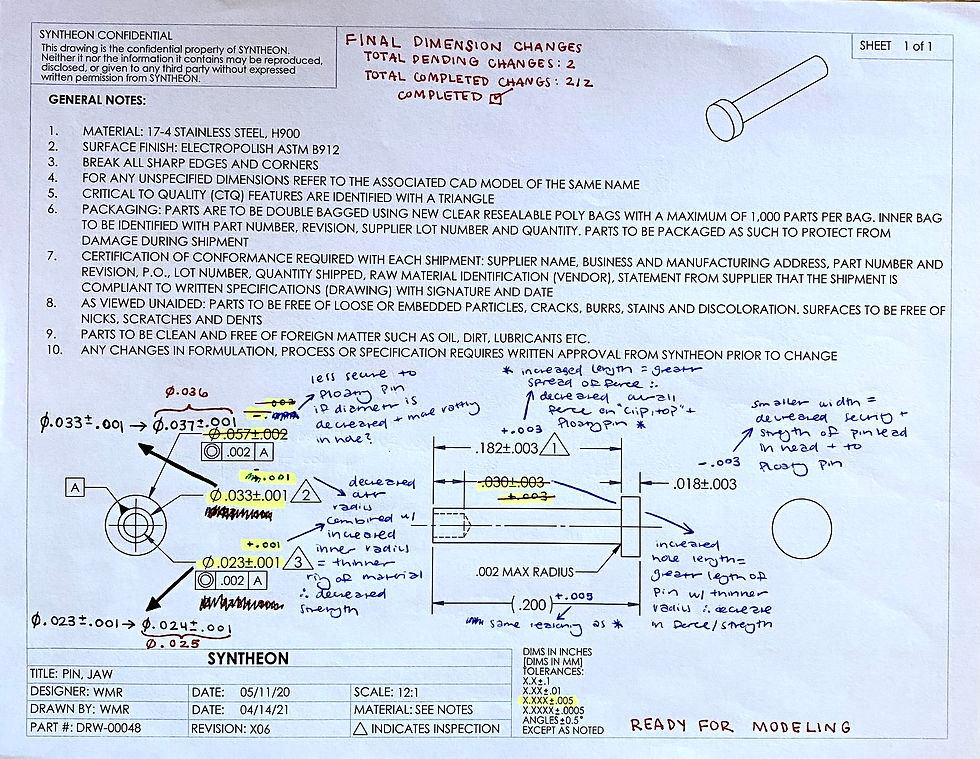

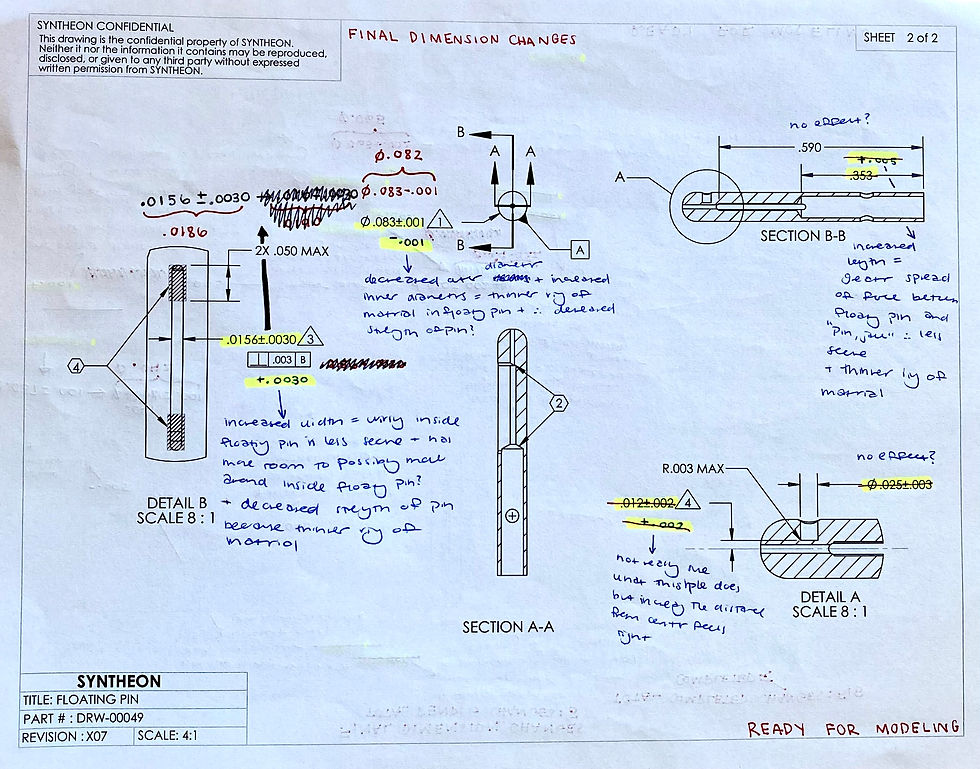






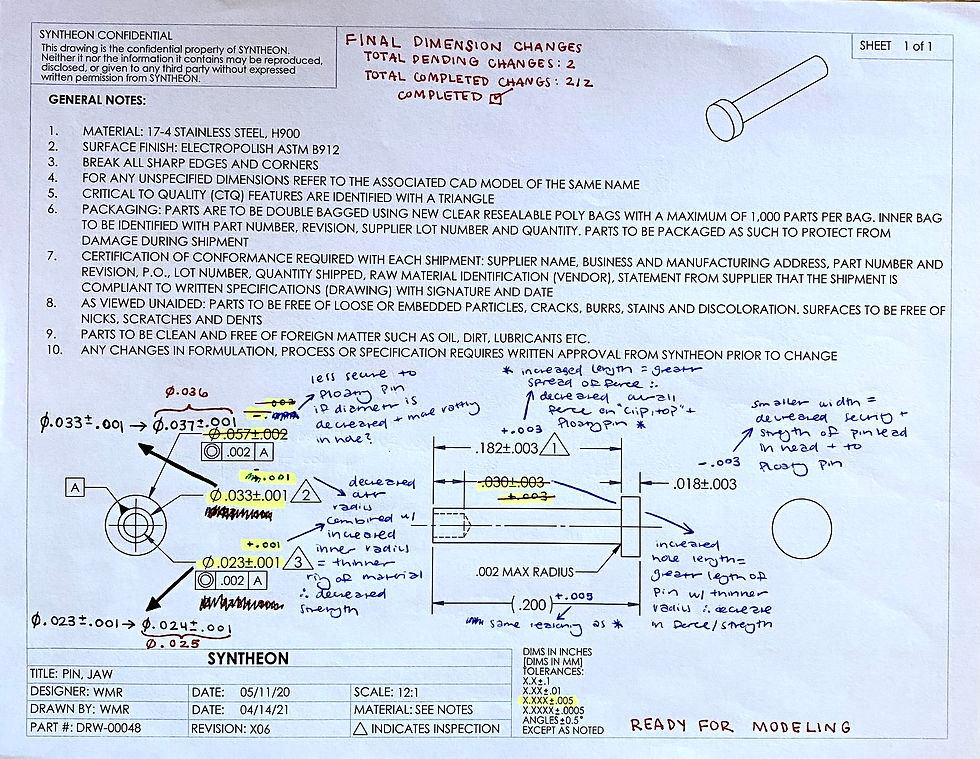

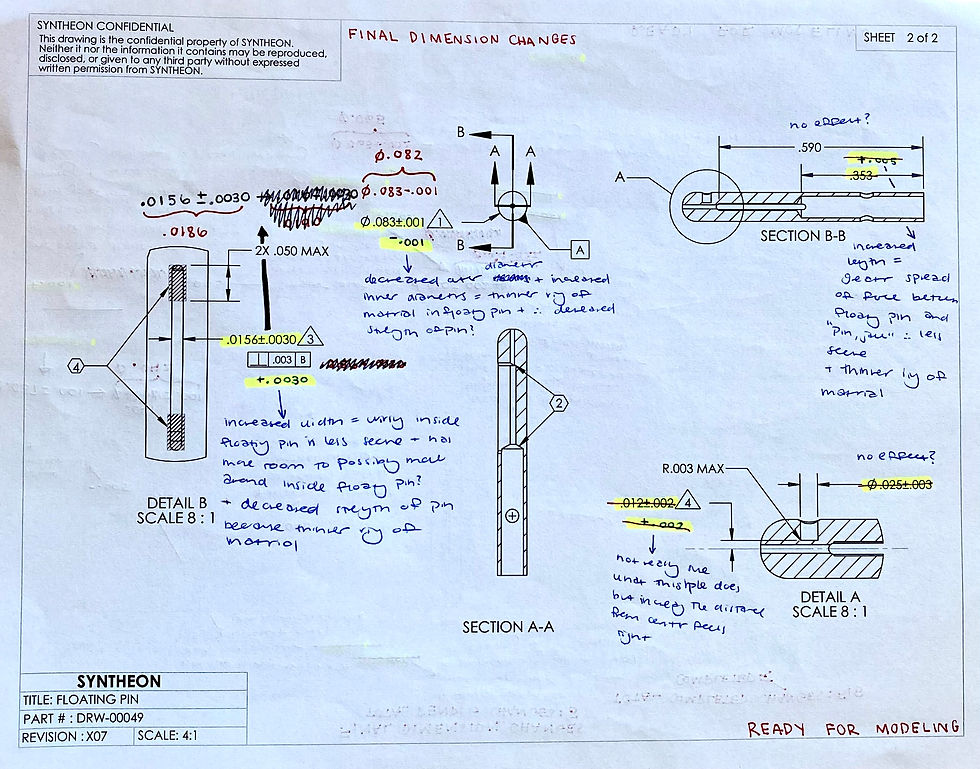






Syntheon llc roar pump Reference drawing & solidworks modeling
As a Mechanical Engineering Intern at Syntheon LLC I independently modeled a pre-existing IV pump including a cylinder & cap to hold IV fluids for use in ROAR pump design verification as well as in general SOLIDWORKS assemblies. During this modeling project I took measurements for the pump, cylinder, & cap to draw a plethora of technical references before modeling. I then utilized SOLIDWORKS CAD to model the pump, cylinder, & cap as well as put them in an assembly.





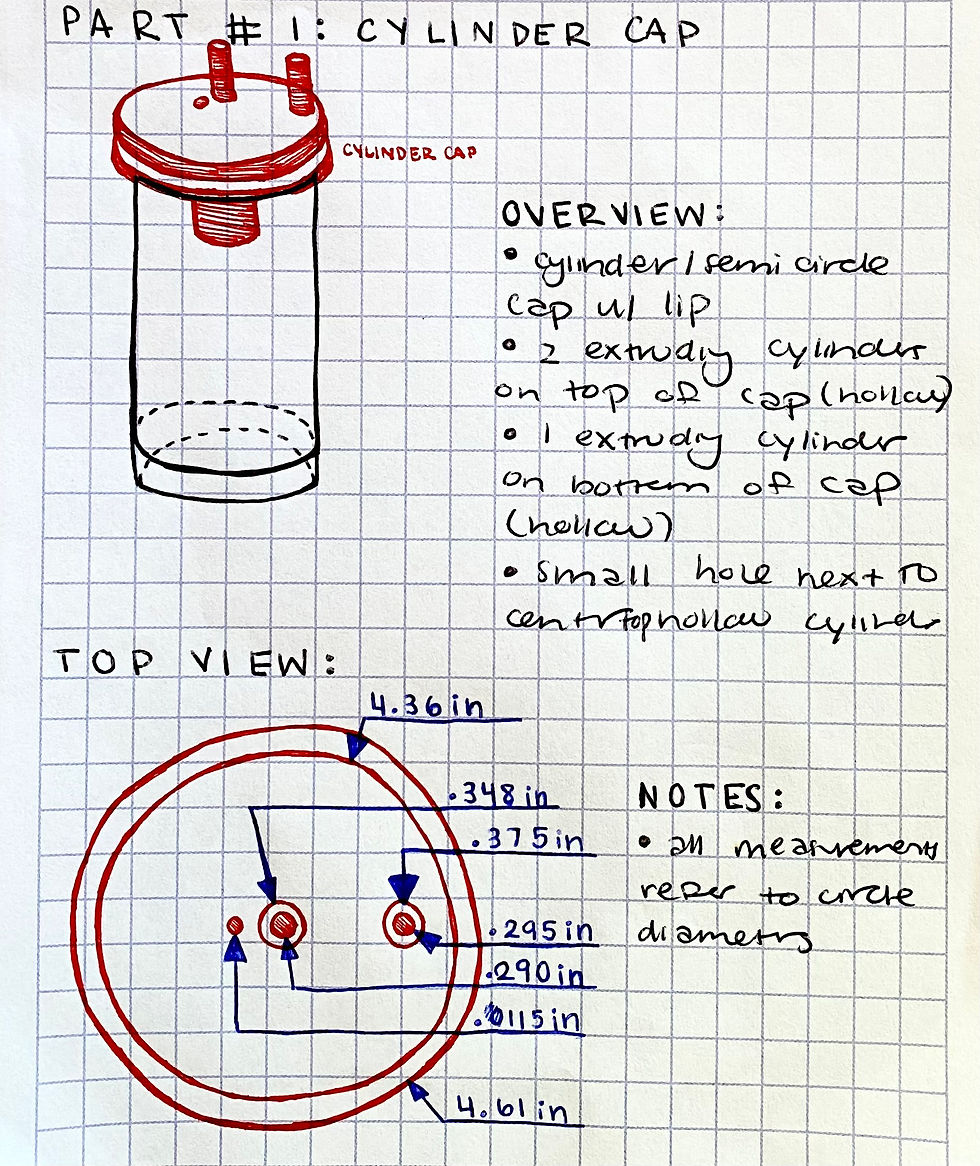



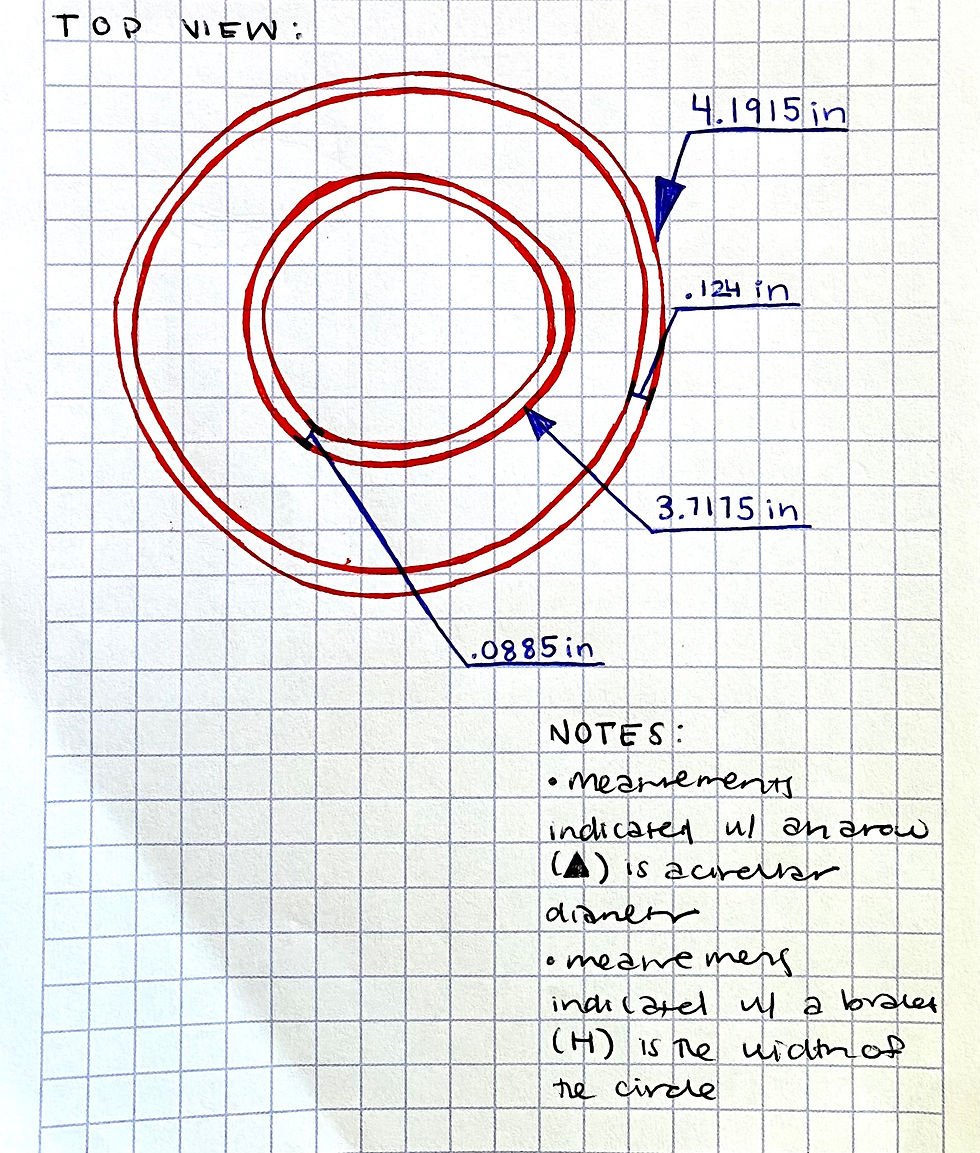







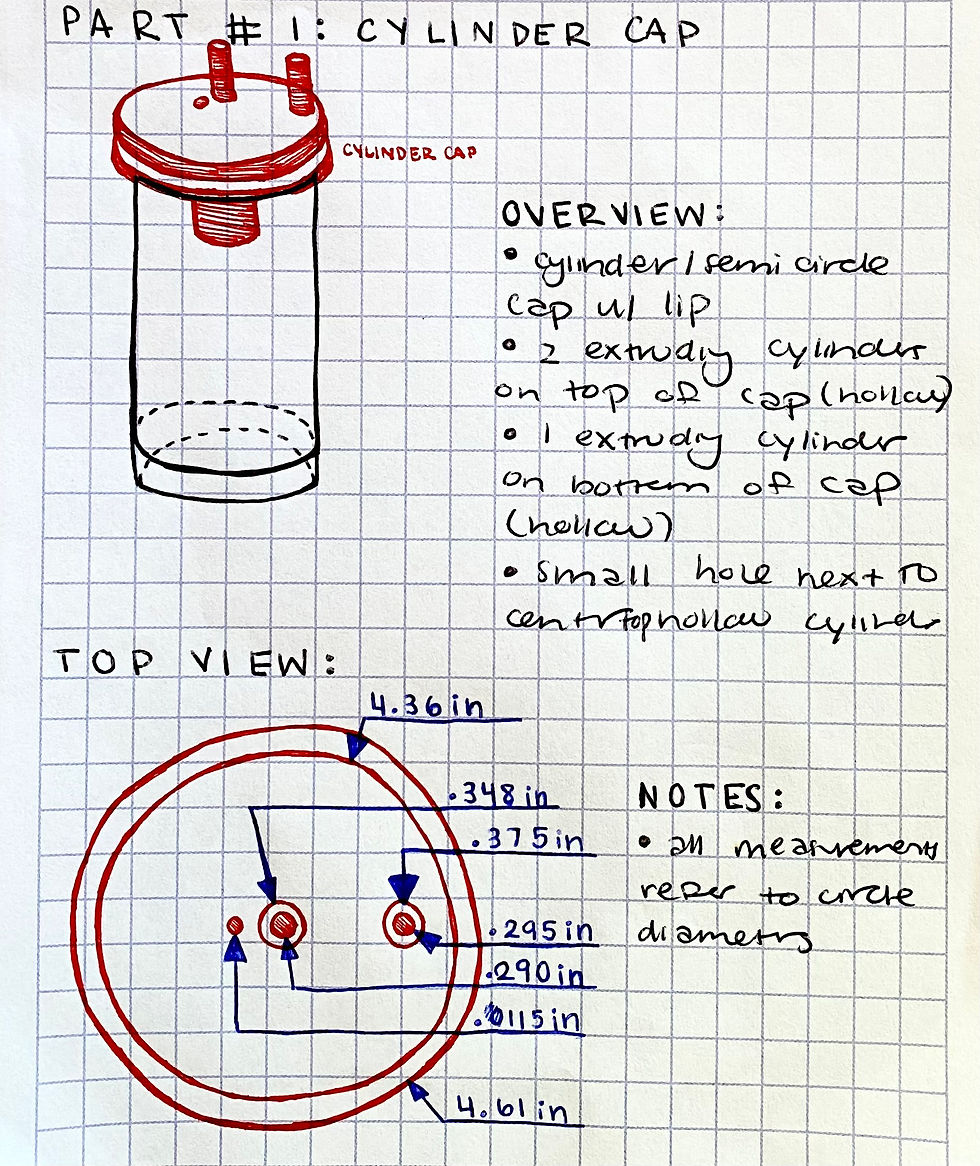



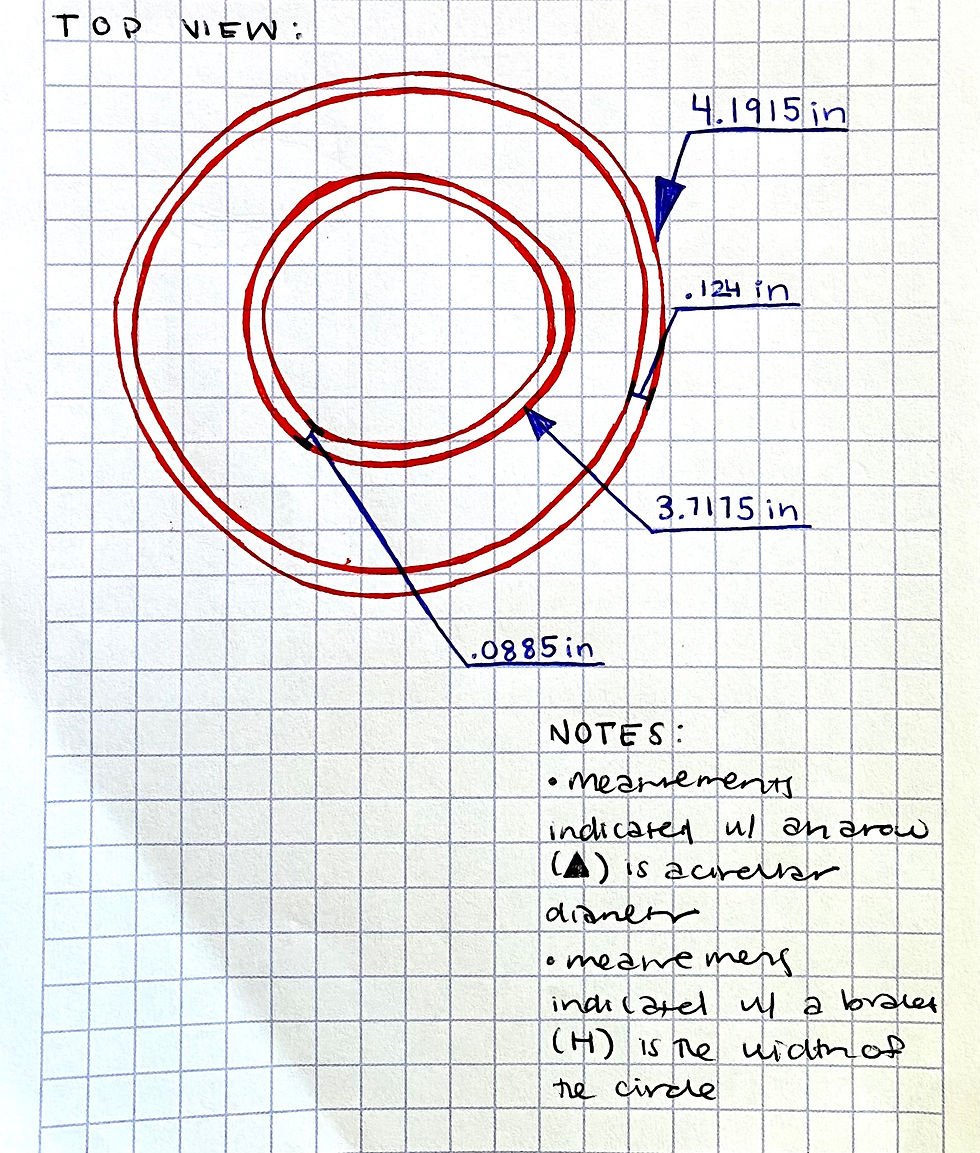

